The origins of the Indian cement industry can be traced back to 1914 when the first
unit was set-up at Porbandar with a capacity of 1000 tonnes. Today India has 142
large cement plants and more than 360 mini cement plants. However, the industry
is dominated by around 20 companies, which account for almost 70% of the total cement
production.
Technology Up-gradation:
Technological upgrades involving more efficient and cleaner technologies acquired
by the Indian cement industry in the past few years has brought in capability to
produce different types of cement like Ordinary Portland Cement (OPC), Portland
Pozzolana Cement (PPC), Portland Blast Furnace Slag Cement (PBFS), Oil Well Cement,
Rapid Hardening Portland Cement, Sulphate Resisting Portland Cement, Clinker Cement,
White Cement, Low heat cement, High early strength cement, Hydrophobic cement, High
aluminium cement, Masonry cement etc.
Currently, over 90% of the total installed capacity is based entirely on the modern
and environment-friendly dry process technology. Co-generation of power utilizing
waste heat is an added advantage of introduction of new technology which has resulted
in substantial savings of energy and fuel for this highly energy intensive industry.
Cement Industry, which was branded as the highest polluter of environment, now meets
the pollution standards, and is no longer a polluter today. It contributes to environmental
cleanliness by consuming hazardous wastes like Fly Ash (around 30 MT) from Thermal
Power Plants and the entire 8 MT of Slag produced by Steel manufacturing units every
year.
Business scenario:
Cement is a commodity business and sales volumes mostly depend upon the quality
perception and distribution reach of the company. There is intense competition with
players cashing in on quality and expanding reach to achieve pan India presence.
The per capita consumption of cement in India is approximately 60% below the world
average and is almost 7 times lower than that of China. This underlines the tremendous
scope for growth in the Indian cement industry in the long term.
Owing to the fast pace of economic reforms and a major thrust from the government
on the infrastructure sector, the real estate sector is booming and there is a flurry
of activities in infrastructure development such as the emerging trend of building
concrete roads, expansion of the state and national highways as well as projects
to build reliable Transport Systems like the Mass Rapid Transport Systems in all
major metro cities. All this is leading to tremendous growth in the cement industry.
The Industry recorded an exponential growth with the introduction of partial decontrol
in 1982 culminating in total decontrol in 1989. The push in cement demand during
the last fiscal was attributed to revival of infrastructure and real estate projects.
The central government has earmarked US$ 47 billion for infrastructure development
during fiscal 2011-12. This thrust on infrastructure will keep the long term demand
for cement intact.
Demand-Supply scenario:
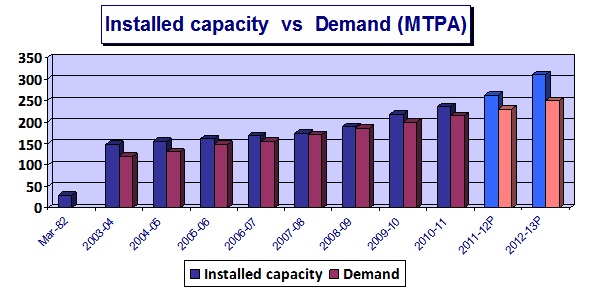
Today, India is ranked second among the world cement producing countries. The Indian
cement industry has clocked production of more than 100 MT for the last five years,
registering a growth of nearly 9% to 10% year on year.
The total cement production for Apr-Jan 2010-11 was 137 MT as compared to 131 MT
during the corresponding period of the previous fiscal.
Globalization:
Cement and gypsum products have received cumulative foreign direct investment (FDI)
of US$ 2,315.58 million between April 2000 and January 2011, according to the Department
of Industrial Policy and Promotion (DIPP).
Top cement companies of the world are vying to enter the Indian market, thereby
sparking off a spate of mergers and acquisitions.
Among the domestic players, Gujarat Ambuja taking over DLF Cements & Modi Cement
and acquiring 14% stake in ACC; ACC taking over IDCOL; India Cement taking over
Raasi Cement and Sri Vishnu Cement; and Grasim's acquisition of the cement business
of L&T, Indian Rayon's cement division, and Sri Digvijay Cements, are some examples
of consolidation in the Indian cement industry.
Given the high potential for growth, foreign cement companies are picking up stakes
in large Indian cement companies. Swiss cement major Holcim has picked up 14.8 %
in Gujarat Ambuja Cements (GACL) leading to the formation of Holcim-ACC-Gujarat
Ambuja Cements combine. The other leading player is the Aditya Birla group combine
through Grasim Industries and Ultratech Cement. Lafarge, the French cement major
has acquired the cement plants of Raymond and Tisco. Italy based Italcementi has
acquired a stake in the K.K. Birla promoted Zuari Industries cement plant in Andhra
Pradesh, and Heidelberg Cement of Germany has entered into an equal joint-venture
agreement with S.P.Lohia Group controlled Indo-Rama Cement.
Issues concerning Cement Industry:
Cement, being a bulk commodity, freight accounts for over 17% of the costs, and
transportation over long distances can prove to be uneconomical. Availability of
limestone, availability and quality of coal, licensing of coal and limestone reserves,
supply of power from the state grid and high government levies on cement are the
main cause of concern for the industry. Added to this, the high levels of capital
investments needed for capacity expansion, modernization and up gradation of the
cement industry have long gestation periods.
However, given the sustained growth in the real estate sector, the government's
emphasis on infrastructure and increased global demand, it looks as if the juggernaut
of cement industry would continue to roll on the path of growth.
Role of ERP in Cement Industry:
Oracle Enterprise Resource Planning (ERP) software provides a companywide business
visibility interlinking all functional areas such as sales and distribution, manufacturing,
purchasing, inventory, finance & accounts, human resource development etc. and works
on a unified Customer database and a single Supplier database for the entire company.
It is designed to work based on the best business practices prevalent in the industry
the world over.
Data security is addressed thru a comprehensive portfolio of security solutions
deployed by Oracle and using privileged user access controls provided thru system
administrator.
Details are available at:
Oracle Database Security
All major business processes practiced in the industry can be mapped in Oracle ERP.
The entire cement manufacturing process starting from raw material preparation,
clinker production and finish grinding of clinker can be mapped in the Oracle Process
Manufacturing (OPM) module of the Oracle ERP system. It works seamlessly integrated
with the other modules such as OPM Product Development, OPM Process Planning, Oracle
Purchasing, OPM Inventory, Oracle OPM Costing, OPM Order Management, and OPM Financials
of the Oracle E-Business Suite.
Design formulation: Simulations can be performed in Oracle ERP to
create new Formulations and Recipes or to revise existing ones, in line with engineering
changes. Accuracy is maintained since these can be created or edited by Formulator
only.
Planning: Oracle Flow Manufacturing, Oracle Order Management & Shipping
Execution and Oracle FinancialsBased on the Sales demand and existing recipes, ORACLE
ERP plans purchases of ingredients and other input materials (material planning)
and also performs scheduling of production orders thru resource capacity planning.
Purchasing & Inventory: Purchase Orders are approved as per predetermined
hierarchy and history tracking is maintained. As and when material is received from
Supplier in the ERP system against the relevant order, inventory stocks are updated
for the respective item. Simultaneously, excise registers are updated and / or MODVAT
claim process is completed in the system automatically.
Production: Batches are created against scheduled production orders.
Inventory stocks of Purchased Items, Work-In-Process items and Finished Goods get
updated automatically in the software based on Batch completion (production booking)
done.
Maintenance: Assets are maintained thru a Manual work order or thru
a Preventive Maintenance Schedule (PMS) which automatically generates Preventive
Maintenance Work Orders as well as Material Requirements for the required spare
parts. Based on completion status of such Work Orders, Maintenance Cost is calculated
by the Oracle ERP software.
Quality: Data capture and traceability of Batch / Lot quality right
from input material to finished goods is taken care of by the software.
Invoicing: Finished Goods are invoiced and dispatch documents generated
using the software thus keeping a record of each dispatch against the related Sales
Order.
Sales & Marketing: Besides booking Sales Orders and getting real time
updates on dispatch status of orders booked earlier, the sales team can take informed
decisions on prospective sales orders or formulation of sales strategies sitting
in their respective sales office / regional office / corporate office, based on
the real time stock status of finished goods and estimated date of dispatch of goods
planned for manufacturing.
Excise & Taxation: Excise registers are automatically maintained and
available for on-line review. Sales Tax claims / returns can be filed based on the
system records.
Finance & Accounts: Apart from routine financial transactions such
as receipts from customers, payments to suppliers and cash flow management, financial
books can be maintained and financial reporting can be done efficiently. Product
cost sheets are maintained on-line. Period closing activity in Oracle ERP enforces
system discipline thru periodic inventory and account reconciliations, thus minimizing
major gaps at a later stage. Statutory audits, Tax audits and Cost audits can be
done on-line.
In addition to providing a user-friendly environment, the Oracle ERP software can
be tailored to incorporate specific needs of companies both large and small, progressively
expanded, in the ‘horizontal’ sense to embrace additional organizational functions,
as well as ‘vertically’ to integrate other stages of the production process.
On account of its modular structure, the ORACLE ERP software can cater to cement
industries of all kinds, from vertically integrated companies to those specializing
in single stage of the production process.
On the whole, ORACLE ERP helps to drive the entire organization on a single platform,
provides an improved supply-demand linkage with remote locations, enables informed
management decisions based on real time access to accurate data, and enables cutting
down of material and resource wastages thru effective utilization as well as thru
reduction of communication gaps and paperwork.
For its clients in the Cement industry, the ERP solution package which Filix recommends
includes the relevant Oracle E-Business Suite (Release 12) modules namely, OPM Product
Development, OPM Process Planning, Oracle Purchasing, OPM Process Execution, OPM
Quality, OPM Inventory Control, Oracle Order Management, OPM Logistics, Oracle Enterprise
Asset Management and Oracle OPM Financials.
The main components of this packaged solution are:
- Product Development - Formula, Recipe & Laboratory Management
- Process Planning - Raw material planning & Production scheduling
- Purchasing - Formula, Recipe & Laboratory Management
- Process Execution - Production Management & Process Operations Control
- Quality management
- Inventory management
- Enterprise Asset Management - Breakdown & Preventive Maintenance
- Order Management - Sales & Marketing
- Logistics - Dispatch
- Financials - Account Payables, Account Receivables, Process costing & Manufacturing
Accounting Controls, Cash Management, Fixed Assets & General Ledger
Additionally, on need basis, clients can also opt for Oracle Transportation Management,
Oracle iSupplier Portal, Oracle HRMS and Oracle Business Intelligence products.
Filix has wide ranging experience from end-to-end implementation to post-implementation
support in the Indian Cement industry. Clients utilizing Filix services benefit
from our knowledge base and rich experience in implementing all the above mentioned
modules, mapping of the client business processes with the standard Oracle product
functionality as well as from Filix expertise in development of Customized forms
and reports.
Users of Oracle Financials at these clients benefit from this core strength of Filix
team. This includes, to name a few, handling of complex India localization and taxation
scenarios of Service Tax and TDS, Budgeting, Fixed Asset depreciation scenarios
and making the users comfortable in using the Oracle Financial Statement Generator
to analyze the financial data such as expense, income, taxes, inventory and project
wise expenses.
Customized Reports like Item Cost Report, Material Flow report for OPM Inventory,
Material Consumption report for OPM Inventory, Certificate of Analysis, AP to GL
Reconciliation Report, AR vs COGS Reconciliation Report, Receipt/Purchase Register,
Sales Register, are only a few out of the list of reports developed to suit specific
needs of our clients from the Cement process industry.
With its custom-built products which integrate seamlessly with the Oracle E-Business
Suite application, Filix has deployed its technical expertise to map typical business
processes being practiced at clients.
With its custom-built products which integrate seamlessly with the Oracle E-Business
Suite application, Filix has deployed its technical expertise to map typical business
processes being practiced at clients.
Implementation approach:
Filix services are available for the ‘big-bang approach’ as well as for the ‘staged
approach’ for ORACLE ERP implementation, based on client’s business needs. However,
Filix recommends the 'staged approach' for its prospective clients in the Cement
sector in India. This approach helps to get the basic business processes (Purchasing,
Inventory Management, Manufacturing and Finance) mapped and working in ORACLE ERP
before moving on to utilize the larger benefits such as Business intelligence etc.
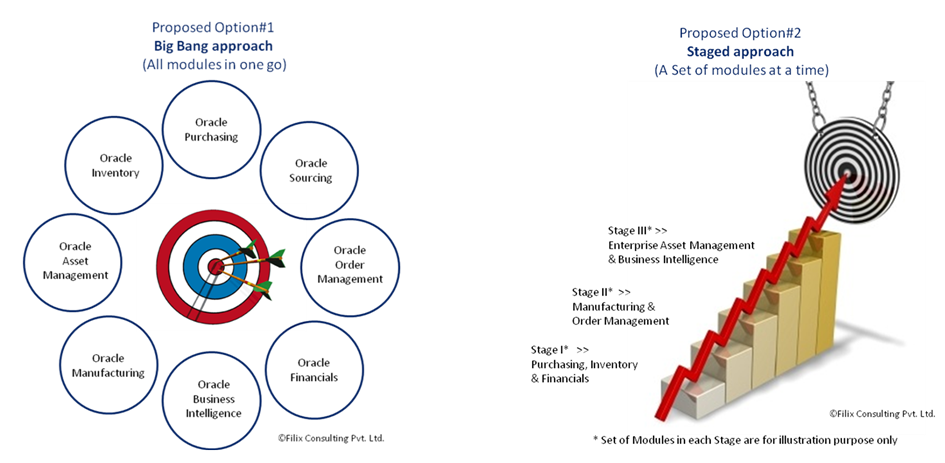